How do I maintain and clean a beaming machine
Proper maintenance and regular cleaning of a beaming machine are essential to ensure its optimal performance and longevity. Here are some general guidelines for maintaining and cleaning a beaming machine:
Always refer to the manufacturer's guidelines and instructions for maintenance and cleaning specific to your beaming machine. They will provide the most accurate and detailed information for your particular model.
Conduct routine inspections of the machine to identify any signs of wear, damage, or loose components. Check for loose wires, misaligned optics, or any other issues that may affect performance. Address any problems promptly to prevent further damage.
If specified by the manufacturer, apply lubrication to the machine's moving parts according to the recommended schedule. Lubrication helps reduce friction and wear, ensuring smooth operation.
Clean the optics and beam delivery components regularly to maintain their performance. Use lint-free wipes or lens cleaning solutions recommended by the manufacturer. Be gentle when cleaning to avoid scratches or damage to the surfaces. Avoid touching optics directly with your fingers.
Remove dust, dirt, and other debris from the machine regularly, as they can affect the beam quality and machine performance. Use compressed air or a soft brush to remove loose particles. Take care not to dislodge or damage any sensitive components during the cleaning process.
If your beaming machine has a cooling system, ensure it is well-maintained. Clean or replace filters as recommended, and check for any blockages or leaks in the cooling channels. Maintaining proper cooling is crucial for the machine's performance and longevity.
Periodically inspect the electrical connections and wiring of the machine. Ensure that all connections are secure, and there are no loose or damaged wires. If you notice any issues, consult the manufacturer or a qualified technician for assistance.
Regularly verify the operation of safety features such as interlocks, emergency stop buttons, and safety shut-off systems. Ensure they are functioning correctly and respond appropriately when activated.
Depending on the machine's usage and manufacturer's recommendations, schedule periodic professional servicing or maintenance. This may involve more in-depth inspections, calibrations, or adjustments that require expertise and specialized tools.
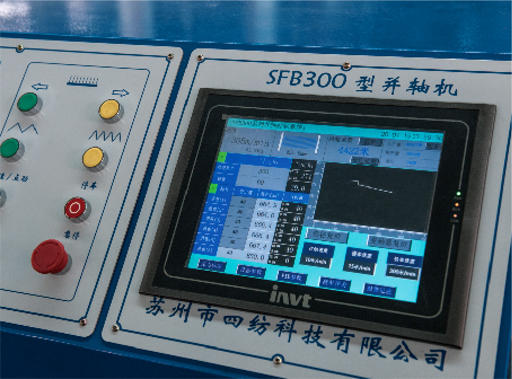
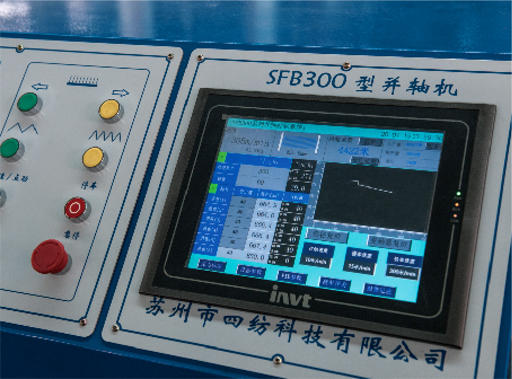